Best Practice: Pressure Gauges Part - 2
Best Practice: Pressure Gauges - Part 2
In last week’s blog we examined some of the most common pressure gauge issues we’ve heard from the field, covering overpressure, pressure spikes, and reduction of mechanical vibration and pulsation. This week serves as part two of our pressure gauge best practices, with four additional guidelines to ensure optimized performance of your industrial pressure gauges.
Resolve Gauge Temperature Problems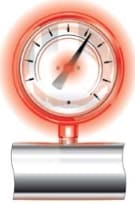
Symptom: A breakdown of the gauge components; discoloured dial or liquid case fill.
Possible Cause: The gauge is incorrectly mounted or located too close to system media or accessories; the wrong gauge type has been selected (a Bourdon tube style gauge may not be the best fit for the application).
Possible Result: Elevated temperature stresses the pressure system and affects measurement accuracy; system media is released into the environment, resulting in media loss and potential injury.
Possible Solution: Select a gauge with a different temperature range to accommodate the possible range the system will see; for high-temperature applications, choose a diaphragm seal solution in a non-316 stainless steel alloy.
Prevent Gauge Corrosion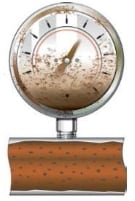
Symptom: A corroded pointer; discoloured liquid case fill; buildup in case; fogged window.
Possible Cause: Contaminants are getting inside the case (the fill plug is missing; the case or window is cracked).
Possible Result: Contaminants cause corrosion of the Bourdon tube; contaminants inside the gauge window result in an inaccurate reading or inability to read the gauge; system media is released into the environment, resulting in media loss and potential injury.
Possible Solution: Select a gauge with a liquid case fill or with a hermetic seal to keep contaminants out; use a diaphragm seal solution in a non-316 stainless steel alloy for increased corrosion resistance.
Avoid Gauge Clogging
Symptom: A zero pressure measurement on the gauge while the system is operating.
Possible Cause: Media that is highly viscous, crystallizing, hardens, or contains particles or solids clogging the socket orifice.
Possible Result: A completely inoperable gauge or one that shows no pressure (as no system media or pressure is reaching the Bourdon tube).
Possible Solution: Select a gauge using a diaphragm seal for greater flow area; in cases of solidification at lower temperature, add heat tracing or insulation to maintain media movement; add filtration to system upstream.
Take Proper Care of Gauges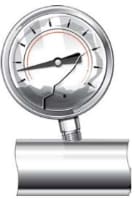
Symptom: A cracked or missing window; leaking case fill; missing back plates or fill plugs; heavy external buildup on case.
Possible Cause: No effective maintenance program in place, resulting in old or neglected gauges; insufficient training on gauge maintenance; the gauge has been placed in a location susceptible to damage.
Possible Result: Accelerated degradation and corrosion of the internal gauge components affect gauge performance.
Possible Solution: Establish a program to replace failed gauges; increase the amount and depth of training on gauge maintenance; select a more durable gauge to better withstand a longer service time; for applications with heavy buildup, use a gauge cover to protect the gauge; evaluate system design to relocate the gauge.
The performance and longevity of your pressure gauges relies on system design, correct product selection, and on-going maintenance. Need help with system design, application support, or product selection? Give us a call today -> 403-243-5646
Industrial Pressure GaugesPressure Gauges for Panel Builders