Keep Ahead of the Curve
Return to Main
Pressure regulators are highly technical, specialized fluid handling components. The process of selecting the correct regulator requires definition of the application according to pressure requirements, flow rate, gas/liquid composition and temperature. Proper selection can help avoid undesirable conditions such as droop and creep. Poor selection can lead to failures such as improper pressure control and contamination of gas streams.
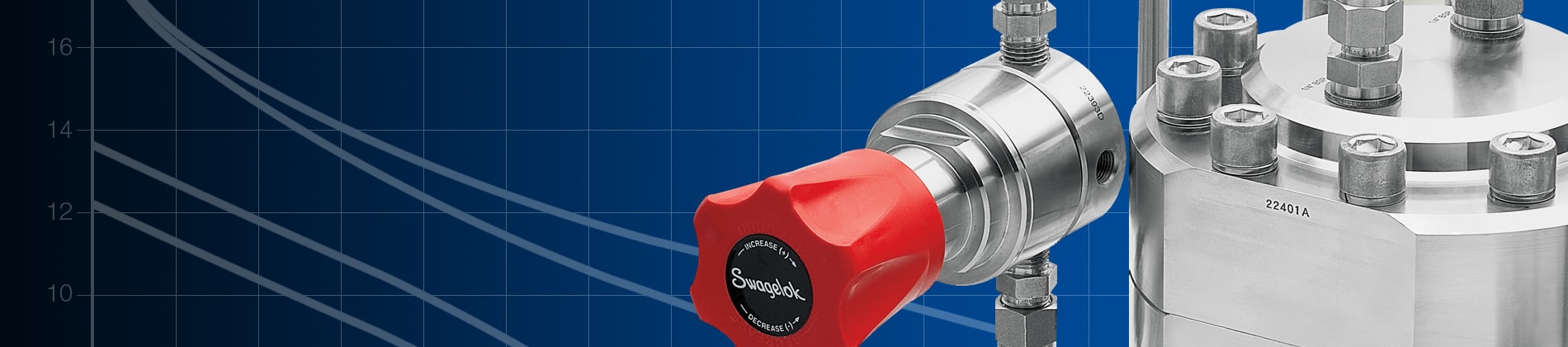
Pressure Reactive
There’s a lot going on inside a pressure regulator – it’s always adjusting along its specific range of capabilities to meet your application requirements – which makes the process of selecting the correct regulator all the more imperative. Equally important is the ability to foresee and troubleshoot issues if and when they arise. Let’s talk about fluid specific gravity and flow as an example.
Manufacturers usually create gas flow curves using air or nitrogen. If the system media is a different fluid, it may be necessary to adjust the flow scale to account for the difference between the specific gravity of the actual system (Gactual) and that of the fluid used to create the curve (Gref). The effect of specific gravity changes the flow rate by a factor (FG):
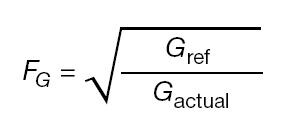
As an example, Hydrogen’s correction factor is 3.8, meaning 3.8 molecules of hydrogen have the same volume as one molecule of air. Therefore, the point on a flow curve showing an airflow volume of 100 std ft3/min (2,831 std L/min) indicates a comparable hydrogen flow of 380 std ft3/min (10,760 std L/min), a significant difference that needs to be fully understood and accounted for in order to avoid performance issues.
Anticipate the Curve(ball)
If you’re responsible for configuring pressure regulators for your system, you know there’s a long list of application variables that need to be considered. The list of potential application issues is equally long. We’ve outlined some of the more common problems and troubleshooting below:
Problem: |
Outlet pressure creeps up without turning the knob. |
Potential Cause: |
Damaged valve and/or seat. |
Potential Solution |
Replace cartridge. |
Problem: |
Controlled pressure drops off sharply even when the flow is within regulator capabilities. |
Potential Cause: |
Clogged filter element. |
Potential Solution |
Replace cartridge. |
Problem: |
Constant leak through relief hole under the control knob. |
Potential Cause: |
Damaged relief valve seat or regulator mounted in wrong position. |
Potential Solution |
Assemble new relief valve seat or mount regulator in the correct position. |
Problem: |
Required outlet pressure cannot be reached. |
Potential Cause: |
Inlet pressure not high enough. |
Potential Solution |
Ensure sufficient inlet pressure. |
Problem: |
Outlet pressure rises too much moving from dynamic to static situation. |
Potential Cause: |
Too much flow in dynamic situation. |
Potential Solution |
Check specific application data against flow curves in Swagelok documentation. |
Problem: |
Outlet pressure does not drop if adjustment knob turned clockwise. |
Potential Cause: |
Non-venting regulator. |
Potential Solution |
Open shut-off valve in outlet line to reduce the outlet pressure. |
Problem: |
Outlet pressure changed without turning adjustment knob. |
Potential Cause: |
Changes to inlet pressure result in changes to outlet pressure. |
Potential Solution |
Maintain constant inlet pressure to regulator. |
Problem: |
Constant leakage from outlet before relief set pressure reached. |
Potential Cause: |
Damaged valve and/or seat and/or seat o-ring. |
Potential Solution |
Replace valve and/or seat and/or o-ring. |
Problem: |
Required set pressure cannot be reached. |
Potential Cause: |
Inlet pressure not high enough. |
Potential Solution |
Ensure sufficient inlet pressure. |
Problem: |
Leakage between body and spring housing or through relief hole at side of spring housing or through 1/8” NPT connection on body. |
Potential Cause: |
Damaged o-ring or insufficient torque on spring housing. |
Potential Solution |
Replace o-ring or tighten spring housing according to specifications. |
Problem: |
Inlet pressure rises too much when going from static to dynamic situation. |
Potential Cause: |
Too much flow in dynamic situation. |
Potential Solution |
Larger regulator is required. Check specific application data against flow curves in Swagelok documentation, if available. |
Problem: |
Regulator will not relief at set point. |
Potential Cause: |
Valve is sticking or adjustment knob is accidentally adjusted. |
Potential Solution |
Replace valve or re-adjust adjustment knob. |
Problem: |
Set pressure has changed without turning adjustment knob. |
Potential Cause: |
Changes to outlet pressure result in changes to set pressure. Increase of outlet pressure will result in fall of set pressure. Decrease of outlet pressure will result in rise of set pressure. |
Potential Solution |
Maintain constant outlet pressure on regulator. |
Problem: |
Regulator certifications required. |
Potential Solution |
Certifications vary depending on geographical location and specification of regulator application. Contact your Swagelok distributor to discuss your regulator needs and certification requirements. |
If you’re thrown a regulator curve ball, or need help selecting the appropriate pressure regulator for your application, we want to help. Contact one of our knowledgeable associates, or review our additional regulator resources - Flow Curve Generator, Pressure Regulator Selection Strategy White Paper, and Webinar Replays - here:
Pressure Regulator Resources
Return to Main